
Corrugated Basics
If you are new to purchasing corrugated, this section is for you! It gives you some of the lingo and pictures of what the terms mean.

Quick Video Overview - Details Below
Cardboard vs. Corrugated
Cardboard is a thick paper stock that you would typically see used for cereal boxes. Corrugated is made up of layers of paper that include inside and outside liners with fluting between them


Box Structure
Corrugated fibreboard has two main components: the linerboard and the medium. Both are made from paper called containerboard. Linerboard is the flat facing that adheres to the medium. The medium is the wavy, fluted paper in between the liners. There are four main types of corrugated board:
Single Face: One medium is glued to one liner. Typically used as a wrapping material.
Single Wall: The medium is between two liners. Also known as double face. The outside liner is smoother than the inside liner.
Double Wall: Three liners with two mediums in between. The outside medium is more compact than the inside medium. Used for heavy items which require increased protection and box rigidity.
Triple Wall: Four sheets of linerboard with the three mediums in between.
Flutes: The medium waves are called flutes. The direction and the distance between the flutes provides varying levels of stacking strength and/or cushioning. Generally, larger flute profiles deliver greater vertical compression strength and cushioning. Smaller flute profiles provide enhanced structural and graphics capabilities for retail packaging
.
Box Styles
The styles of boxes Tilsner Carton Company can make for you are endless, but the most common ones are listed below.
​
Regular Slotted Container, RSC
This is the most common box style. All flaps have the same length, and the lengthwise flaps meet at the center of the box when folded.
​
Half Slotted Container, HSC
Same as Regular Slotted container without one set of flaps.
​
Full Overlap Container, FOL
All flaps have the same length, the width of the box. When closed, the outer flaps come within one inch of a complete overlap.
​
Five Panel Folder, FPF Center Seam
This "econo" folder is a single cut and scored piece that wraps around the contents and is sealed.
​
Telescope Boxes - Container With Cover.
These boxes have a separate top and bottom that fit over each other.
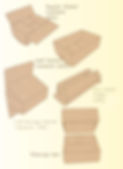

Box Measurement
Box sizes are measured using the inside dimensions. Using the order of length, width and height. For example, the box on the left has an interior dimension of Length 23 5/8" x Width 15" x Height 14 1/8". (23 5/8" x 15" x 14 1/8")
​

BMC - Box Manufacturers Certificate
The bottom of the box carries a seal, the Box Manufacturers Certificate, BMC. It indicates the strength of the board and the weight limit.
The strength of corrugated board defines how much weight a box can withstand, and is determined based on a strength test.
There are two recognized tests.
1. Burst Test/Mullen Test - This measures the pounds per square inch needed to rupture the board from internal or external forces.
2. The Edge Crush Test, ECT -This measures the top and bottom compression of the corrugated board. This is a primary factor in predicting the compression strength of a completed box. The higher the number, the stronger the box.



Printing On Corrugated Can Be Tricky
Colors change due to the printing method (flexo, digital and litho-label) the color they are printed on (kraft, mottle...) and the grade of the surface. We can help you manage colors and how they interact.
See our Art Guidelines Page.
Flexo Printing
Flexography is the most common process used to print packaging. The corrugated is pulled through a series of stations, or print units. Each print unit is printing a single color. The various tones and shading are achieved by overlaying basic shades of ink.
This technology employs plates with raised images and only the raised images come in contact with the corrugated during printing.
Our flexo presses accommodate sheets up to 63" x 126", and shorten production time by slotting, scoring, folding and gluing. The highest line screen is 71.
Our onsite ink kitchen saves time and ensures consistency
​
Litho Label Lamination
As an alternative to printing directly on corrugated, the lithographic process offers crisper images and enhanced color flexibility by printing onto large or small labels that are then mounted onto corrugated.
The basic principle of offset printing is that oil and water do not mix. A litho printing plate has non-image areas which absorb water. The plate is kept moist throughout so that ink only adheres to image areas.
During every cycle of the press the ink image is first transferred to a rubber surfaced offset cylinder and from there to the paper.
The offset cylinders flexibility preserves the delicate plates and conforms to the surface of textured papers.
Tilsner Carton Company has several laminating machines that apply the litho labels to corrugated. We have the capability to do full or spot label mounting up to 81" x 81" Our maximum sheet size is
81" x 121".

Digital Printing
Digital printing is ideal for short run needs as well as prototyping and proofing. It eliminates the expense of printing plates.
Our digital printer has 8 colors. In addition to CMYK colors it has light black for neutral grays and orange for more Pantone® coverage and skin tones.
A gloss or semi-gloss look can be obtained. The inks are UV-curable pigmented ink that offers flexibility on scored areas. The resolution is 600 dpi.



Joint Options
Gluing
Stitching
Taping

Money Saving Ideas
Auto-locking bottoms can save time and money. Our Design Team can recommend additional ways to save you money! (Right sizing your packaging, protective inserts...).
